AUTHOR | DATE CREATED | VERSION | DOCUMENT NUMBER |
---|---|---|---|
Dr. Gerard McGranaghan | 10 July 2014 | V1 | CC11 – 00034 |
Introduction
This report measures the differences in emitted heat flux between hollow and plain infrared heating elements. Of particular interest is the effect of a reflector placed at the rear of the elements on the emitted infrared output.
Method
Two types of heating element were tested FTE650W and FFEH600W. These were placed in the Herschel and analysed using the 3D Infrared heat flux mapping routine. In this automated system, an infra-red sensor is robotically guided around a pre-determined coordinate grid system in front of the heater element under test. The sensor is a Schmidt-Boelter Thermopile Heat Flux Transducer with a design maximum heat flux level of 2.3 W/cm2 and measures infrared (IR) in the band 0.4-10 micrometres. The incident radiant heat flux recorded at each point is then saved and post processed to give a 3D representation of the infra-red heat flux emission. The coordinate system is a 500mm cubic grid in front of the heating element, see Figure 1. The robot moves the sensor in 25mm increments along a serpentine path in the x and z directions, while the heating element is mounted on a slide carriage which increments in 100mm steps along the y direction.
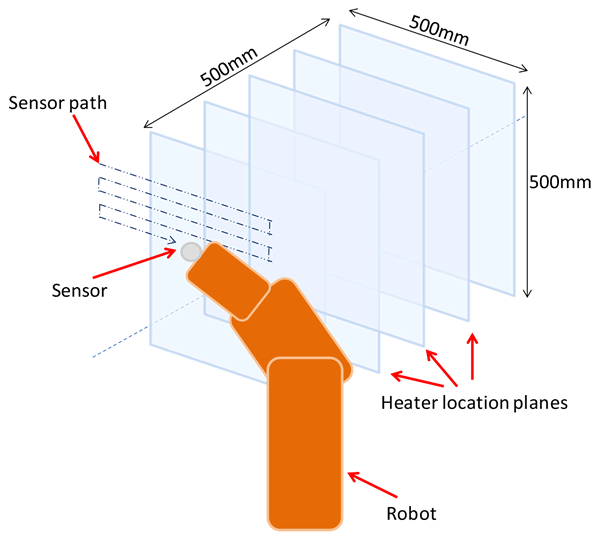
Results
FTE 650W with and without reflector
To start with, the standard FTE650W with a standard aluminised steel RAS1 reflector was measured in the Herschel over a 500mm cubic grid. The results are shown in Figure 2. At a distance of 100mm, the Herschel heat flux sensor measures 48.4% of the 650W input energy emitted from the heater, this comes to around 314.7W. The maximum heat flux recorded at 100mm from the heater was 0.69 W/cm2 while the heat flux profiles are semi- elliptical in the horizontal direction and semi-circular in the vertical.
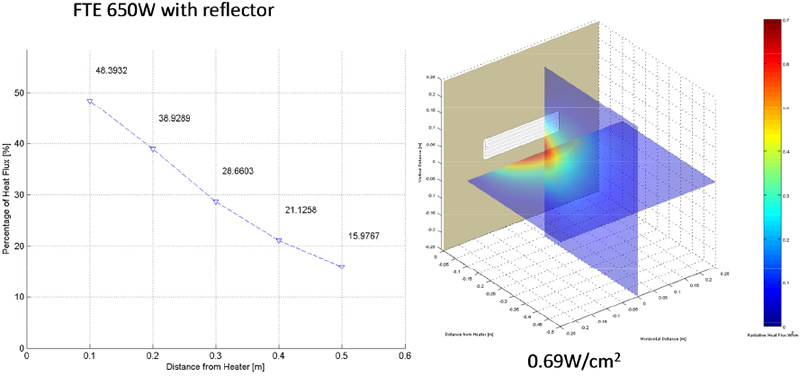
Next the reflector was removed from the rear and the test repeated. The measured percentage of radiation detected reduced from 48.4% to 34.4% as shown in Figure 3. This is a drop of around 29% of the radiated heat output with a reflector. The peak heat flux also reduced sharply from 0.69 W/cm2 to 0.37 W/cm2.
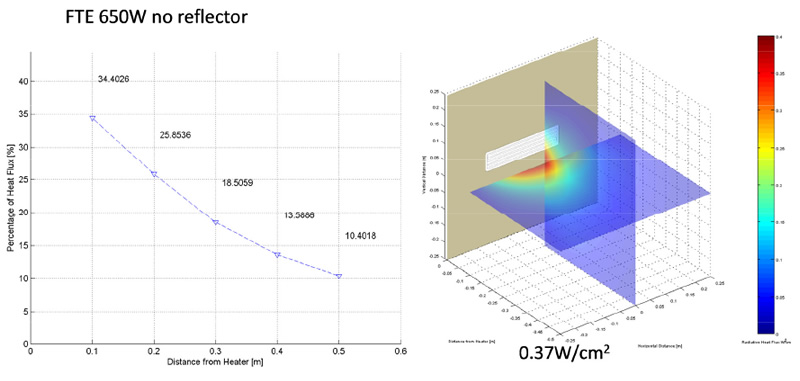
FFEH 600W with and without reflector
The same test was then carried out with the hollow element, type FFEH 600W, the results of which are shown in Figure 4. Note that the input power is 50W less than that received by the FTE650W.
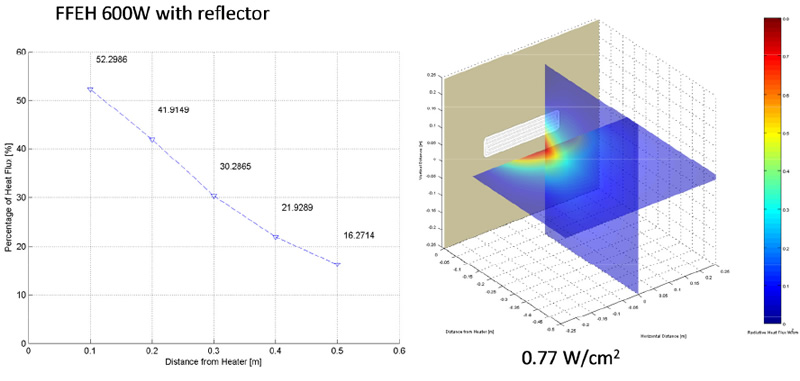
Despite the reduction in power consumption, the FFEH provided a greater efficacy of infrared output returning 52.3% at 100mm. This meant that 313.7W was detected as infrared emissions from the front face of the FFEH600W, one watt lower than the standard FTE650W element. The maximum heat flux also rose to 0.77 W/cm2 as opposed to 0.69 W/cm2 for the FTE650W while the horizontal 3D heat flux remained semi elliptical in profile. However the vertical profile was not semi-circular but of a more pronounced elliptical form which helps account for this higher peak heat flux value. Therefore the FFEH 600W gives almost the same output as an FTE 650W element, and also a higher peak heat flux thanks to its narrower elliptical heat flux profile.
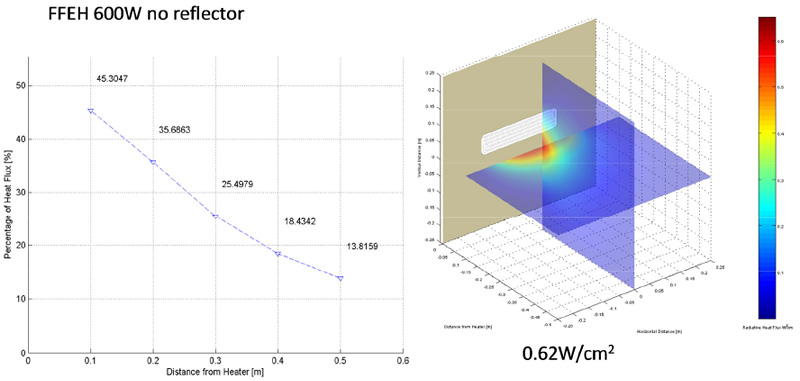
When the reflector was removed from the rear and as can be seen in Figure 5, the test repeated the performance of the FFEH element at 100mm decreased from 52.3% to 45.3%, a drop in performance to 14% of that when a reflector was used. This was not as severe as the 29% drop seen when a reflector was removed from the FTE element. Therefore a hollow element without a reflector, it will not suffer to the same extent as an FTE element without a reflector.
As also indicated in Figure 5 the 3D heat flux remained semi-ellipsoid in profile. However it was weaker in infrared output as indicated by the peak heat flux value dropping from 0.77 W/cm2 to 0.62 W/cm2.
Conclusion
If an FTE or FFEH element is operated without a reflector, emitted radiation in the forward direction will decrease. Peak heat flux will also decrease.
If a hollow element is used without a reflector, it will not suffer a drop in performance to the same extent as using an FTE element without a reflector.
The FFEH 600W gives almost the same infrared output as an FTE 650W element, and also a higher peak heat flux thanks to its narrower elliptical heat flux profile.
[Download not found]Note
Due to the present method of orienting the sensor, the percentage of radiation detected from the heaters as quoted here is actually lower than their true efficiency. However, as a back to back comparison, the tests are very valid.
These tests were carried out on single elements, and radiative characteristics will change when multiple elements are used in arrays. The findings are nonetheless indicative.